Gravity Pour for Consistent Quality Castings
When your industrial application requires castings with high structural integrity and superior mechanical properties, gravity pour permanent mold casting is an ideal solution. As a leader in manufacturing dimensionally challenging, complex, and pressure-tight/leak-tight castings, gravity pour permanent mold casting has been a staple of Le Sueur Incorporated’s business for over 60 years. Our aluminum casting longevity has resulted in outstanding supplier relationships, from Minnesota and beyond.
We are committed to exceeding our customers’ expectations by manufacturing high-quality aluminum castings. Our fully gated and documented product launch procedures include project development that can uncover potential issues before production begins.
Permanent Mold Gravity Casting Experts
LSI has state-of-the-art permanent molding machines including low pressure and gravity/tilt pour, allowing us to meet various customer requirements. Our internal quality capabilities also include:
- Complete metallurgical lab
- NDT lab
- Three x-ray processes
- Liquid penetrant inspection
- In-house heat treating
LSI is a full-service supplier ensuring that our customers receive consistent quality products and services. LSI pours many alloys including A356, 356, 319, 333, C355, 355, and 413.
Advantages of Tilt / Gravity Pour Permanent Mold Casting
- Permanent mold castings offer superior mechanical properties (yield, tensile, and elongation) than conventional casting processes
- Overall part quality is improved
- Improved surface finish
- Tighter tolerances are achieved than conventional sand castings.
- Spray coatings (insulating and chill coatings) are easier to apply in the mold resulting in improved overall part quality.
- Tighter tolerances in permanent mold often result in less machining and lower overall costs compared to sand casting
Gravity Pour Permanent Mold Casting Process
Gravity pour permanent mold casting utilizes gravity to pour molten metal into iron or steel molds having the reverse image of the part being produced. The molten aluminum can be poured using one of two methods: directly into the mold (static) or via pouring cups with the mold slowly shifting position during the pour (tilt pour). Magma casting simulation is used to determine the best technique for filling the casting. The cavity is filled through a gating system and solidifies after several minutes. The mold is then opened, and the aluminum casting is ejected from it.
This process is also known as tilt pour permanent mold, semi-permanent mold, gravity die casting, static permanent mold, permold, and permanent mould. The permanent mold process is very stable and repeatable resulting in a consistent quality casting.
Semi-permanent mold is an iron or steel mold utilizing sand cores to create complex geometries that cannot be formed by just the mold. Cores can be made from the shell core or isocure core making processes. Cores are placed in the mold prior to the metal being poured. Semi-Permanent Mold = An Iron or Steel Mold + Sand Core(s).
Static Pour Permanent Mold Casting vs. Tilt Pour Permanent Mold Casting
As the name implies, static pour mold casting involves no movement of the mold. The mold is held vertically while the molten aluminum is poured into it.
For tilt pour casting, once the metal is poured into the pouring cups, the mold is slowly rotated to the vertical position. Under gravity, the metal slowly fills the mold cavity at a constant rate.
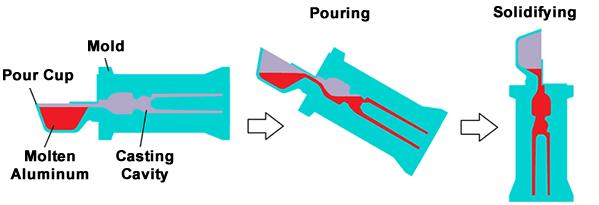
Tilt Pour Permanent Mold Aluminum Casting Applications
Industrial applications that benefit from tilt pour permanent mold casting include:
- Air Cylinders
- Base Castings
- Cold Plates
- Compressor Bodies
- Cooling Fins and Fans
- Couplings
- Covers
- Diaphragm Pumps
- Differential Housings
- Engine Mid Plates
- Filter Bases
- Gear Box Housings
- Gear Cases
- Heating Elements
- Hydraulic Cylinders
- Oil Pans
- Pistons
- Pressure Housings
- Suspension Components
- Transmission Channel Plates
- Transmission Housings
- Transom Base Mounts for Marine Applications
- Valve Bodies
- Valve Housings
High Quality Permanent Mold Gravity Casting
As a global supplier of high-quality aluminum castings with over 70 years of experience, LSI is your trusted source for exceptional gravity pour permanent mold castings. We also offer complete in-house precision machining, finishing, and assembly.
Discuss your gravity mold casting project with us or start designing your mold casting today.